Chongqing Jinyu Longitudinal Shearing Slitting Machine Manufacturer Branch Sales Point: Kangning Road, Hexi Industrial Park, Laoshan District, Chongqing, China Tel: 332 Contact: Wu Manager slitting host is the highest precision equipment in metal slitting line. The number and spacing of the disc blades on the shaft can longitudinally cut the strip fed continuously after the unwinding of the web into a plurality of narrow strips, which are then re-rolled into coils by a coiler. Depending on the thickness of the strip, the number of slitting narrow strips is from several to several tens, and the minimum width of the narrow strip should be greater than or equal to the thickness of the disc insert. In Europe in the late 16th century, first in Germany, and later in Belgium and the United Kingdom, human-driven rolling mills for roll-rolling soft metal sheets were produced. In the 17th century, there was a rolling mill for water-driven rolled steel sheets. In 1578, Bulmer obtained the earliest patent of the slitter in the United Kingdom, which used a disc blade on two cutter shafts to cut the soft metal slab longitudinally into strips. In 1590, De Bosch made the first such slitter in Dartford, England. After more than 400 years of development, the most common shape of the slitter is composed of the base, the movable frame, the upper and lower cutter shafts, the fixed frame and the transmission. The slitting machine can divide its precision into ordinary and precision grades. Cutting ordinary cold-rolled carbon steel strips, generally using ordinary grade slitting machines; shearing non-ferrous metal strips, and soft steel strips such as tinplate, usually thin and soft, easy to produce burrs when shearing, should be used Precision grade slitting machine. The horizontal gap between the upper and lower blades during slitting is only 7% to 10% of the thickness of the strip. For example, a steel strip with a thickness of 0.3 ram is slit, the blade gap is 0.03 ram, and the aluminum strip of the same thickness is slit, the blade gap is 0.02 mm, and the overlap of the upper and lower blades is 0.15 mm. On a slitting machine, there are often more than 20 pairs of blades with the B, ix, i-~ material for slitting and slitting, to ensure that each pair of blades has accurate horizontal gap and overlap, which is to ensure the quality of slitting shear. The necessary premise. Therefore, in order to obtain good shear quality and shear accuracy, the slitter should first have sufficient rigidity for its fixed frame and movable frame to ensure accurate positioning of the cutter shaft. The base of the slitter should also have sufficient strength and rigidity to prevent warping deformation when the slitter is lifted or moved. The precision of the slitter is finally reflected on the cutter shaft, which not only requires good strength and rigidity of the cutter shaft, but also the parallelism of the upper and lower cutter shafts, the rotation precision of the cutter shaft, and the accuracy of the insert and the spacer. Very high demand. It can be said that the precision of the precision slitting machine is comparable to the precision of the metal cutting machine. 1. Precision of the cutter shaft The accuracy of the slitter is mainly reflected in the accuracy of the upper and lower cutter shafts. In the longitudinal shearing, the cutter shaft not only receives the shearing force acting up and down, but also the axial component of the shearing force. 2. Arrangement and pre-tightening of the cutter shaft rolling bearing In order to achieve the above-mentioned cutter shaft accuracy requirements, in addition to the precise addition of the cutter shaft and related parts, it is necessary to pay sufficient attention to the configuration and pre-tightening of the rolling bearing on the cutter shaft. Precision grade slitting machines should adopt P4 or P5 precision rolling bearings and take pre-tightening measures. Even for ordinary grade slitting machines, if they are mainly used for cutting strips with thickness less than 1mm, precision grade rolling bearings should be used and Preloaded. The so-called pre-tightening is to apply a certain preload to the bearing when the rolling bearing is installed, to eliminate the working clearance of the bearing, and to generate pre-deformation at the contact between the rolling element and the inner and outer rings, so that the contact area of ​​the working surface is increased, thereby improving the bearing. Support stiffness and rotation accuracy. All in all, it is the measure of internal interference when the rolling bearing is not subjected to external loads. Preloading is divided into axial preloading and radial preloading. The configuration and preloading of the slitter cutter shaft bearing are similar to those of a metal cutting machine. On the fixed frame of the slitting machine, the bearings close to the working part of the cutter shaft are usually installed in pairs of tapered roller bearings or double-row cylindrical roller bearings with inner diameter and taper, and the radial adjustment is eliminated by axial adjustment. The gap achieves a radial preload. The outer end of the cutter shaft generally adopts a pair of angular contact ball bearings and is axially pretensioned. Because the speed of the slitter cutter shaft is not high, the temperature rise of the bearing during operation is not high, and the axial force to be subjected to the reasonable arrangement of the cutter is not very large. Therefore, it is only necessary to select the diagonal contact of the medium pre-tightening degree. The ball bearing can be. Such a pair of angular contact ball bearings take into account the amount of axial deformation generated under preloading of the bearing during assembly, and the bearing is preloaded after pressing the corresponding end face during assembly. It is also possible to use a two-way thrust angular contact ball bearing which can withstand two-way axial load, has good rigidity and is easy to assemble and disassemble. In addition, the accuracy of the bearing near the working position of the cutter shaft has a greater influence on the accuracy of the rotation of the cutter shaft than the accuracy of the outer end bearing. Therefore, when selecting the bearing precision, the former should be selected a little higher. 3, the accuracy of the blade and the spacer sleeve If the accuracy of the blade and the spacer sleeve (the flatness of the YJ piece and the non-parallelism, thickness tolerance, etc.) is not enough, even the precision cutting machine can not get the ideal shear Quality and precision, so be sure to choose the right blade and spacer according to the user's requirements for slitting accuracy. When the blade and the spacer are used, the skilled cutter must accurately measure the axial dimension and then align the knife up and down to reduce the accumulation error of the blade gap when the knife is matched. The accuracy of the blade and the spacer sleeve has a great influence on the efficiency and accuracy of the knife. The tooling in the slitting operation is extremely technical, and the percentage of working time is quite high. A set of high precision inserts and spacers will greatly increase the efficiency of the fit. 4. Structure of the slitting machine holder 4.1. Slider type holder The slider type is the most common type of holder. The holder of the lower cutter shaft is fixed in the movable frame and the fixed frame, and the upper cutter shaft seat is in the left and right sliders, and the left and right sliders can be parallel to the lower cutter in the guide rails of the movable frame and the fixed frame by the lifting screw The axis moves up and down. There are balance springs under the left and right sliders to eliminate the axial clearance of the lifting screw. After the position of the upper cutter shaft is adjusted, lock the left and right slides with the locking device to eliminate the gap of the guide rail. In order to ensure the parallelism of the upper and lower cutter shafts in the vertical and horizontal directions, the position of the lower shaft is generally fixed, and the cutting position of the strip is reduced after the blade is bluntly sharpened, lower than the belt. The running plane of the material. For this reason, some of the lower cutter cutter holders are also made of a slider type, which can be adjusted up and down to keep the strip shearing position always on the running plane of the strip, but this increases the complexity of the structure and the amount of processing. . In order to eliminate the influence of the screw clearance of the slider lifting screw, some slitting machines adopt a lower-mounted slider structure. The holder of the upper cutter shaft is fixed in two frames, and the holder of the lower cutter shaft is mounted in the slider to adjust only the position of the lower cutter shaft. 4.2. Eccentric tool holders Eccentric tool holders are mostly double eccentric type, that is, the upper and lower cutter shafts are supported in the eccentric sleeve. The upper and lower eccentric sleeves are driven by the synchronous gear shaft to adjust the eccentricity by rotating in the opposite direction, thereby changing the upper and lower knives. The height of the shaft gives a different amount of overlap. The parallelism of the upper and lower shanks of this structure is guaranteed by the machining accuracy of the main parts, including the eccentricity accuracy of the eccentric sleeve, the accuracy of the adjustment gear, and the phase accuracy of the adjustment gear and the eccentric sleeve. If the accuracy level of the adjustment gear is not enough, it is best to take anti-backlash measures. The advantage of the eccentric type is that the outer diameter of the blade is reduced after sharpening, but the shear position of the strip remains unchanged. In addition, since the gap between the eccentric sleeve and the seat hole can be controlled to be small by the configuration, and the structure can provide a large bearing area to withstand the shearing force during the slitting, the knife is removed after the movable frame is changed during the tool change. The shaft does not increase the amount of sag. The disadvantage is that the eccentricity of the eccentric sleeve cannot be very large, thus limiting the sharpening range of the blade. Some slitting machines adopt a single eccentric structure, but the upper cutter shaft is supported in the eccentric sleeve, and the structure is relatively simple. The disadvantage is that the upper and lower tool axis cannot be in the same vertical plane. In addition, this structure also causes the shear position of the strip to decrease after the blade is sharpened, which is lower than the running plane of the strip. 4.3. Adjustable length of the cutter shaft The main feature of this structure is that the movable frame on the left side can be adjusted to a pair of blades near the outermost side of the left end of the cutter shaft, so that the working length of the cutter shaft is shortened, so that the rigidity of the cutter shaft is significantly improved. . This allows a slitting machine to adapt to both large-width thin strip shearing and small-width thick strip shearing. Since the deflection of the cutter shaft is proportional to the cube of the length of the cutter shaft, the cutter with a size of 3x1800mm is adjusted to a size of 1200mm, and the maximum deflection of the cutter shaft is only about one-third of the former. Thus, when the number of cut strips is the same, the thickness of the sheared strip can be increased to 5 mm. 4.4. Swing arm type This structure is to fix the upper and lower cutter shafts on the upper and lower swing arms. Through the forward and reverse spiral adjustment mechanism, the upper and lower swing arms are close to or away from each other to realize the change of the center distance between the upper and lower cutter shafts, thereby adjusting the upper and lower blades. The amount of overlap. A spring is also provided between the upper and lower swing arms to eliminate the influence of the thread gap. This structure is mainly suitable for the slitting of thin strips, and the structure is simpler than the above. The structure of the above four tool holders has its own advantages and disadvantages, but the imported or domestic slitting machines that can be seen at present are all slider type and eccentric type, and the length of the cutter shaft is adjustable and the swing arm The type slitting machine has only been reported and has not been widely used. Precision and high speed are the obvious trends in the development of metal slitting machine technology, and the slitting main machine is the most accurate equipment in the metal slitting machine production line, shortening the auxiliary time of tool change or tooling to improve the production of slitting and dividing lines. Efficiency has obvious effects. It is necessary to establish the above understanding when purchasing slitting slitter, and give enough attention and consideration. For the consideration of production and future development, please choose high-speed production line equipment.
Http://news.chinawj.com.cn
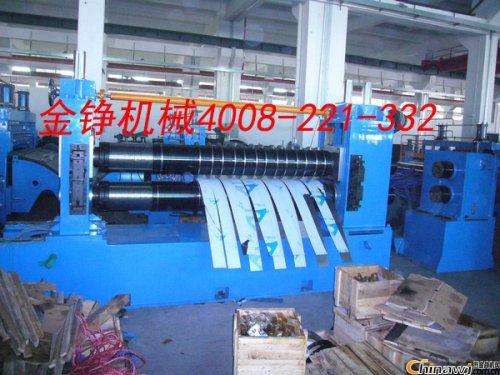
Editor: (Hardware Business Network Information Center) http://news.chinawj.com.cn
DUPLEX STAINLESS STEEL
Duplex Stainless Steels Available
Yuhong Group supplies LDX2101, 2205, Ferralium 255, Zeron 100 and LDX2507 in the form of plate, sheet, strip, bar, pipe, tubing, pipe fittings, flanges and weld wire.
Duplex Stainless Steel Overview
Duplex Stainless Steels, also referred to as austenitic-ferritic stainless steels, are a family of grades with about equal proportions of ferrite and austenite. These steels have a duplex microstructure which contributes to their high strength and high resistance to stress corrosion cracking. Due to their high content of chromium, nitrogen and molybdenum, duplex steels offer good resistance to local and uniform corrosion. Duplex stainless steels have good weldability.
Today, modern duplex stainless steels can be divided into three groups:
Lean Duplex such as LDX2101
Standard Duplex such as 2205, the work-horse grade accounting for more than 80% of duplex usage
Super Duplex such as Ferralium 255 and Zeron 100 and LDX2507
Of the duplex grades, duplex 2205 is the most widely used. However, the super duplex steels like Zeron® 100 and LDX2507 are excellent for servicing severe corrosive environments, such as offshore and marine applications. Lean duplex 2101 is available as an economic alternative to 300 series stainless steels.
What are the Characteristics of Duplex Stainless Steels ?
Very good resistance to uniform corrosion
Very good resistance to pitting and crevice corrosion
High resistance to stress corrosion cracking and corrosion fatigue
High mechanical strength
Good sulfide stress corrosion resistance
Good abrasion and erosion resistance
Good fatigue resistance high energy absorption
Low thermal expansion
Good weldability
In what Applications are Duplex Stainless Steels® used ?
Oil and gas equipment
Offshore technology
Seawater desalination plants
Chemical industry, especially when handling chlorides
Flue-gas cleaning
Desalination plants and seawater systems
Pulp and paper industry
Cargo tanks and pipe systems in chemical tankers
Firewalls and blast walls on offshore platforms
Bridges
Storage tanks
Pressure vessels, reactor tanks, and heat exchangers
Rotors, impellers and shafts
Duplex Steel Welded Pipe
Duplex Steel Welded Pipe,Stainless Steel Welded Pipe,Duplex Steel Butt Welded Pipe
YUHONG GROUP CO.,LIMITED , https://www.alloypipeline.com