1. Heat treatment inspection procedures for carbon steel castings
Considering the complex shape of the valve casting, it is easy to deform and crack, the heat treatment of carbon steel castings is usually annealed. During the inspection, it is important to supervise whether the supplier carries out the following heat treatment specifications and to check the hardness value of the casting.
1. Points of attention when heat treatment of carbon steel castings
Generally, carbon steel castings should pay attention to the following points during heat treatment:
1.1, when the furnace temperature rises to 650 ° C ~ 800 ° C, whether it slowly heats up
Because in the heating process, especially the carbon steel castings with complex shapes, when the furnace temperature rises to 650 ° C ~ 800 ° C, the temperature should be slowly increased, or kept at this temperature for a period of time. Because the carbon steel undergoes a phase change in this temperature range, a phase change stress is generated along with the volume change, and if the temperature rises rapidly, the temperature difference between the thin portion of the casting and the thick portion and the surface layer and the center layer is easily increased, thereby Increasing the thermal stress of the casting easily leads to cracking of the casting.
1.2, is the holding time sufficient?
In order to make the temperature inside and outside the casting uniform, and there is enough time for the tissue to completely transform, the thick-walled castings have a longer holding time than the thin-walled castings.
The calculation method of the holding time is as follows:
a) According to the maximum wall thickness of the same casting, the insulation is kept for 1 hour every 25mm, and it is suitable for castings with a wall thickness of 20mm or less.
b) According to the maximum wall thickness of the same casting, it shall be kept for 1 hour every 50mm, but not less than 2 hours.
c) Calculated according to the height of the pile (ie, the height of the casting pile), the heat preservation time of the general carbon steel castings is calculated by 1m high and 4 hours of heat preservation.
1.3. When carbon steel castings are annealed, they are generally cooled with the furnace.
2. Heat treatment specification for carbon steel castings
Second, austenitic stainless steel castings heat treatment inspection procedures
Austenitic stainless steel castings are usually heat treated and stabilized to provide optimum corrosion resistance. During the inspection, it is important to supervise whether the supplier is carrying out the following heat treatment specifications.
1. Solid solution treatment of austenitic stainless steel
The purpose of the solid solution treatment is to completely melt the carbides in the steel and obtain a single-phase structure by heating the casting to 950 ° C to 1175 ° C. The heating method should be preheated at a low temperature and then accelerated to a solid solution temperature. The process is to reduce the temperature difference between the surface of the steel casting and the core during the heating process. The solid solution holding time is determined by the wall thickness of the steel casting. Generally, the thickness is calculated by the wall thickness of 2.5~3min per mm to ensure that all the sections of the casting are hot through. Yes, it can be quenched into water, oil or air after solid-melt heat preservation, and water is used as usual. Air cooling is only suitable for thin-walled castings.
2. Austenitic stainless steel castings stabilized
In order to prevent the "sensitization" phenomenon of the austenitic stainless steel castings, alloy elements such as titanium and niobium are added to the steel, and after solid solution treatment, the stabilization treatment is carried out, that is, the castings are reheated to 850 ° C to 930 ° C, and after heat preservation, The carbon in the steel is sufficiently combined with titanium and niobium to form a stable carbide.
Concerned about surprises
Label: stainless steel casting
Previous: Use airless sprayer to pay attention to the next article: Extrusion "a porous" technology
We specialize in supplying quality drilling equipments PDC Drag Bit , double cutter pdc Drag Bit , single row cutters pdc drag bit ,3-wings drag bits, 4-wings drag bits, 5-wings drag bits, claw type, clay bits, for mining, water-well drilling, seismic prospecting for many years.
PDC drag Bit Description: Silver solder welded composite sheet, does not fall off and does not collapse. The outer wing of the blade is covered with a half-grain composite sheet to protect the blade from small wear and wear, and the large outlet hole does not contain swarf and quickly discharges cuttings. Multi-blade balance strength, smooth and fast drilling, national standard precision thread buckle, quick and easy loading and unloading, not falling off.
Thread standard: national standardProduct categories: 65mm, 75mm, 91mm, 113mm, 133mm, 153mm, 171mm, 219mm above are the general standards, if you have special needs 311mm,346mm , 490mm, 500mm etc, you can order.
PDC drag bit advantage
1.Small or medium PDC cutter layout.
2. Multiple blade profile dasign,available with round,double laper and parabolic profiles.
3. Various ID flow path desighs provide suffcient cooling and cleaning to whole bit surface.
4. Applicable stratum: soft rock layers such as sandstone, mudstone and weathered rock, with fast footage and long service life.
3 blades PDC drag bit box thread
Double row cutters 5 blades PDC drag bit
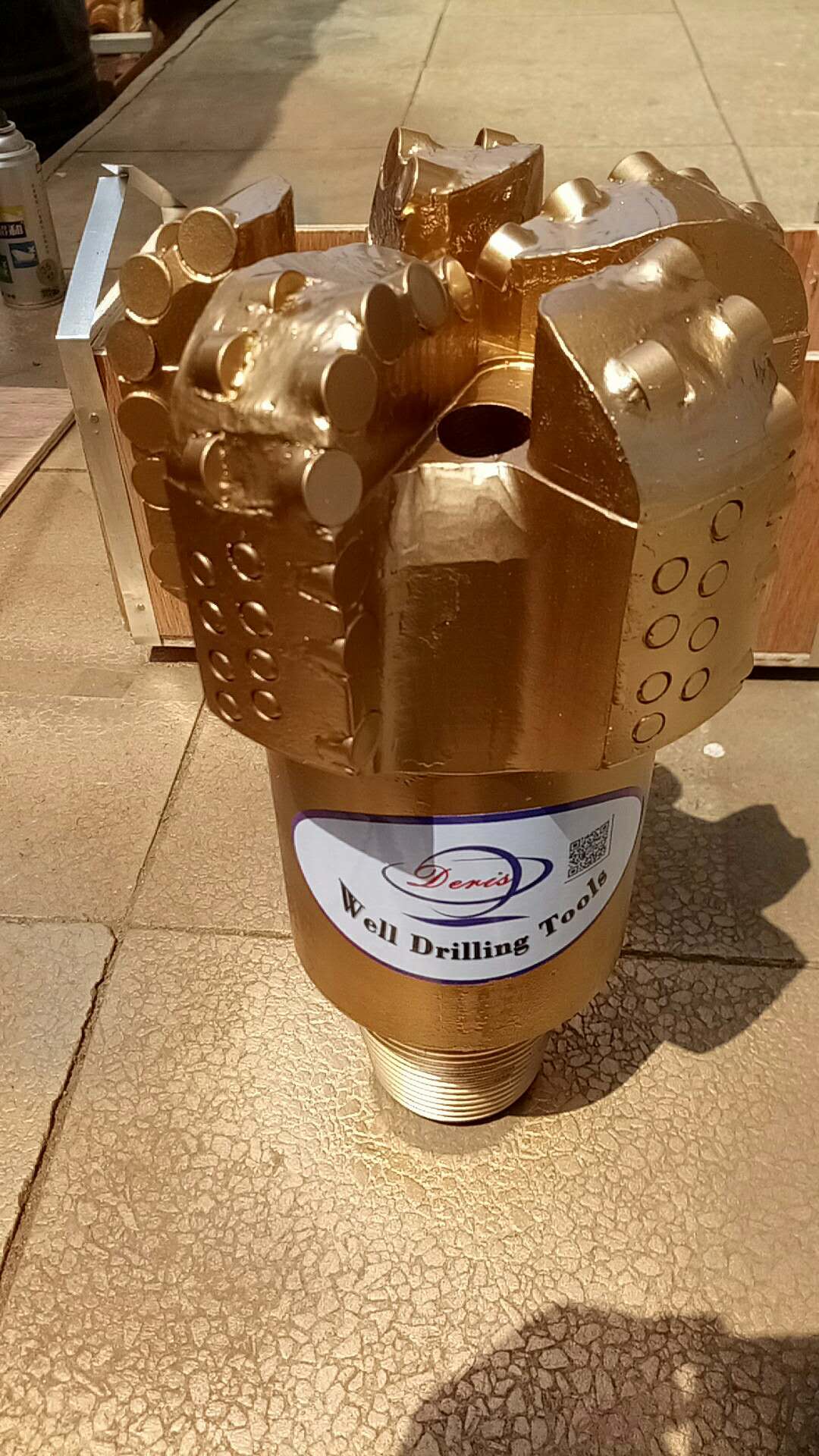
6 blades PDC Bit
PDC Drag Bit
PDC Drag Bit,PDC Drag Drill Bits,Three Wings PDC Drag Bit,4 Blades PDC Drag Bit
Hejian Deris Petroleum Drilling Equipment Co.,Ltd. , https://www.welldrillingbit.com